FAQ
FAQ
We are often asked why we started Carbon Fiber Recycling (CFR), what is different about our process, and what our partners can expect from working with us. CFR’s Founder, Doug Griffin, explains the important role the company plays in reshaping the carbon fiber industry.
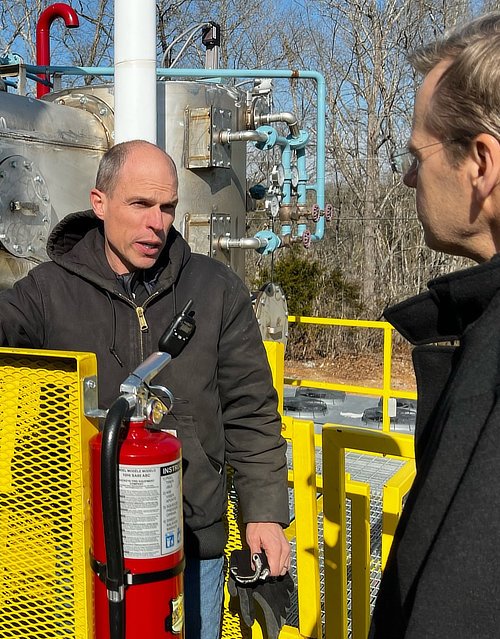
Why did you start Carbon Fiber Recycling?
Humans are amazing creatures, capable of incredible achievements and technological innovations that continuously improve our standard of living, safety, and longevity. The downside of those great accomplishments is the growing burden on the planet’s resources and the ancillary problems of dealing with ever increasing waste streams that are more damaging, last longer and will ultimately derail progress and endanger the planet if new ways of managing them are not found.
The proliferation of high quality carbon fiber composites is a perfect example. Carbon fiber has incredible properties, and its use in myriad products grows rapidly every year. It’s been used to create lightweight and stronger items such as aircraft, spacecraft, wind turbine blades, motor vehicles, and a wide array of sporting and consumer goods. Light weight items use less fuel to start or stop, lift and move, and require less of a foundation to build, hold up, or span. The downside, besides its high cost, is when carbon fiber products come to the end of their useful life, or when manufacturing processes create waste carbon fiber scrap, there is no good environmentally friendly manner to deal with them.
Today these products are dumped in landfills. Because they don’t decompose like other materials, their rapid accumulation will inevitably cause larger problems for the world as time goes on. This requires the creation of methods that either return these items back to their constituent components, or prepare them for reuse in a recycling loop in an environmentally and economically friendly manner.
I’ve been involved in the management of waste products my entire professional life and I’ve always been focused on developing new methods for recycling the volume we park away in landfills that simultaneously bring an economic benefit. I saw a huge opportunity in carbon fiber and founded CFR to tackle it.
What is CFR’s process?
Recycling carbon fiber at commercial scale and on a continuous basis is very difficult and has, until now, only been an aspirational concept. A number of companies have achieved good outcomes with small batch processes but those cannot scale well economically. Until now, companies with scalable flow processes have not been able to achieve high enough quality recycled fiber to become sustainable commercial enterprises.
Carbon Fiber Recycling has developed a unique patented economic, and environmentally friendly, continuous flow process that allows the operator of that process to do things that have not been done successfully at commercial scale before.
Our process is flexible. We can take a variety of carbon fiber materials, including dry fiber, pre-pregs, and cured composites. Our factory in Tennessee was built for continuous (24/7) operations, and was designed to produce large quantities of unsized 6 mm random length chopped carbon fibers that have been validated by leading third party laboratories and end users as being consistently over 95% pure, ideal for a large number of commercial applications. In addition, the cost of this recycled fiber is also a fraction of the cost of new fiber.
So you have found a solution for the environmental impact of carbon fiber?
What is most exciting is that we have solved both the environmental harm that carbon fiber landfill creates and the poor economics that recycled fiber has historically been plagued with.
We offer manufacturers of carbon fiber products the first of its kind, environmentally friendly alternative for their waste and end of life products.
We also provide an inexpensive, high quality recycled fiber for many commercial applications. It’s great for the environment and great for the economy.
CFR provides a true high volume alternative to the existing environmentally damaging shipments to landfills but it also offers an attractive economic proposition which allows high tech recycled carbon fiber to be utilized in more products because it is cheaper. The combined knock-on effect our process creates is exciting.
A select group of qualified companies with large carbon fiber material streams will be eligible to license our technology in the future.
How do you do it exactly?
There are a number of the aspects of our process that are highly proprietary. In broad terms, Carbon Fiber Recycling uses a process called pyrolysis which is the act of heating something in the absence of oxygen.
Heating carbon fiber materials in a controlled environment, in the absence of oxygen is the basis for our magic. With a pyrolytic process, materials cannot burn, but instead they volatilize, producing a gas, just like when something evaporates. Because carbon fiber is produced at incredible temperatures, the fiber is unaffected by the temperatures necessary to volatilize the epoxies and the plastic components that the carbon fibers are locked in. The composite materials turn into a gas, leaving the carbon fiber as a liberated solid.
The fiber is extracted from the process virtually intact and can be used again for the manufacturing of new products cheaper than they can be manufactured for with virgin carbon fiber. That’s in part because the energy used to recycle is a fraction of what it takes to create new carbon fiber.
Isn’t the recycling process itself damaging to the environment in terms of energy requirements and the creation of hazardous, volatile by-products?
This is something we care deeply about, and is another exciting aspect of our process. The answer is no. After all, why would you recycle in the first place if the environmental costs of recycling in aggregate (energy requirements, emission profile, hazardous by-products, etc.) outweighed the environmental costs of virgin fiber production, or used fiber disposal. Our entire process was designed to minimize the environmental costs of recycling.
During the recycling process itself, the pyrolysis gas separated from the carbon fibers can be cleaned up by condensing it into two separate fractions: condensible and non-condensible gasses. Condensible gasses can be further broken down into solids and liquids with different temperature levels.
The non-condensible gasses are cooled to atmospheric temperatures and routed back into special burners that extract the calorific value using combustion to create heat energy for the pyrolysis process to continue. In other words, we can run our recycling equipment using those gasses. So far we have found that we can utilize all of the non-condensible gasses from all the carbon fiber materials we have seen in the market to create the heat needed to run our recycling equipment.
The condensible gasses can be turned into liquids and solids. Liquids are made up of oil that is separated and stored. That oil can also be routed to special burners and utilized for heat to pyrolyze additional carbon fiber materials, reducing the need for non-renewable energy sources.
The amount of oil created can change based on the amount and type of materials being processed, but the process affords the opportunity to have excess oil from the pyrolysis process and this oil can be utilized for different tertiary energy uses after the energy required to run the pyrolysis process has been satisfied. The oil created from the process is similar to a high value crude mix, and must be separated from the condensing medium, stored, and if desired, can be further processed into better known hydrocarbon products like diesel fuel or jet fuel. The pyrolysis oil typically consists of about 80 percent the same molecular make-up of diesel fuel oil, with the remaining 20 percent made up of a mix of lighter and heavier fractions in a homogenous oil solution.
Finally, the solid fraction that is generated from the original pyrolysis gas output is captured and stored. Once accumulated, this fraction is re-routed back into the pyrolytic processing unit to be re-cracked, just like at a refinery, in order to create shorter molecular chain hydrocarbons. By doing this CFR transforms the solid fraction into non-condensible gas, able to be consumed for energy in the process, and condensable liquid fuel, also able to be consumed for energy, or can be further refined into things like diesel fuel and other energy products if desired, thus closing the energy loop. All of this makes our process very efficient.
CFR has developed these capabilities to extract carbon fiber from composites, allowing that fiber to be re-introduced into new manufacturing processes from any form of carbon fiber materials cheaply, while simultaneously converting all of the composite material into useable energy products. We continue to develop these technologies to further refine the process and make it even more efficient on a commercial scale.
We also recycle other materials attached to the receipt of carbon fiber materials. Cardboard shipping boxes, pallets, metal components, plastic parts and plastic sheeting are all items that CFR removes from the waste stream and recycles back into the beneficial use product market. It goes along the ideology of finding a responsible method by which to return the amazing technological innovative items that carbon fiber has been created into, back to beneficial use products in an environmentally friendly way.
Carbon Fiber Recycling is committed to the furtherance of this ideology and ways in which to improve its processes as well as the number of items it can recycle from the materials it receives. The days of placing things in landfills must come to an end, one technological and innovative advancement at a time.
What products can you reuse and how do companies work with you?
We make it as easy as we can for our client partners. We can recycle virtually all products that have a high carbon fiber content (greater than 50% by weight). The one exception is that we will not accept products containing any glass fiber, except for extremely limited exceptions, where the fiber can be mechanically removed from the stream and the stream containing the glass fiber consists of a very high volume of material. In such cases, we may be able to create a custom pre-pyrolytic process where we can effectively handle the glass fiber.
We take in dry fiber, pre-preg and composites in all forms. We can handle cured and uncured products; expired pre-preg materials; carbon fiber thermoset and carbon fiber thermoplastics; and depleted carbon fiber bobbins of all thicknesses (must be packaged separately from resin filled products). Products also do not have to be sorted by resin content.
There is no cost to our partners for recycling their products aside from the cost of shipping the materials to us. They are also not required to purchase any of the recycled fiber. All they have to do is send us a sample of the types of products they want us to recycle which we will analyze in our lab. If we can recycle their products, we will enter into a recycling agreement with them, which includes giving us an idea as to volumes and frequency so we can plan accordingly and they can start shipping.
Companies interested in purchasing our fiber can purchase it directly from our facility.
Why is glass fiber an issue for you?
Glass fiber is often used in conjunction with carbon fiber composites for many reasons, some of which include abrasion resistance coatings, cheaper stiffening effects, and it’s simply cheaper to use than carbon fiber.
We see a lot of mixed use materials that have both carbon fiber and glass fiber in the same item. Unfortunately, it’s difficult to separate glass fiber from carbon fiber and do it perfectly all the time on a high volume basis.
The last thing we want to do is contaminate good quality carbon fiber with glass fiber. We don’t sell glass fiber and don’t want to contaminate the carbon fiber materials we do sell with glass fiber. So, we simply don’t run it through our process so we cannot have any issues with the quality of our carbon fiber output.
There are emerging technologies that may solve this issue on a large commercial scale. When that time comes and the technology is reliably consistent on a commercial scale, it’s highly likely we will implement such a capability, thus increasing our waste stream feedstock and diverting more material from landfill.