What’s So Special About CFR’s Recycling Facility in Tazewell, TN?
By Doug Griffin
We started working on this equipment in 2012, and have finally achieved what we set out to do, which is to develop the capability to recycle all carbon fiber materials on a continuous flow basis, producing high quality rCF at a price point that could revolutionize the carbon fiber recycling industry.
We exceeded our goals in our longevity testing, and after successful sea trials, we start full commercial production in January, 2024.
High Quality rCF
There are two main issues that have plagued the rCF industry. The first issue is removing 100% of the epoxies and resin from the recycled fiber, and the second issue is removing the layer of coke that coats the carbon fiber during the pyrolytic process. CFR’s technology has perfected its reactor and fiber polishing technology to deliver the cleanest rCF in the industry.
Quality of the actual fiber is determined in large part by the quality of carbon fiber fed into the reactor. We limit our inputs to composites with 50% CF content and containing no glass fiber. For large orders, companies requiring a particular fiber length can request fiber to spec, and we may be able to accommodate. We test our fiber onsite and have it verified by third parties.
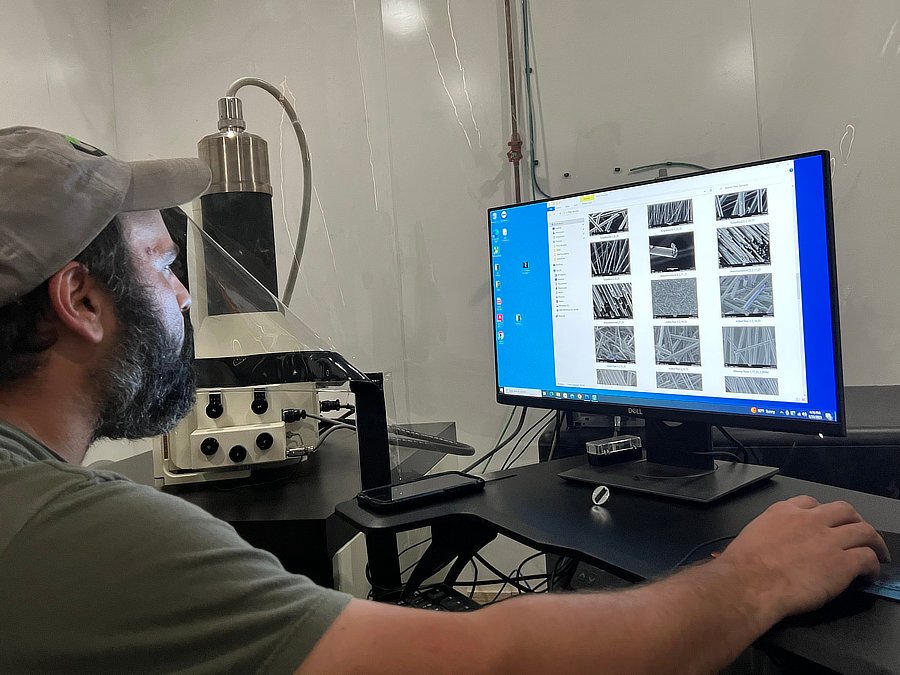
Batch vs Continuous Flow Production
Up until now, the majority of carbon fiber recycling systems have been batch systems. It is quite easy to create a batch system and that is how we started in the early days.
The problem with a batch system is that you can never reach economies of scale because you are limited by the size of the reactor and you are always heating up the reactor, processing, cooling and resetting the system. Batch systems use so much energy, and take so much time to produce a small amount, so your product is just too expensive, and not environmentally friendly.
A continuous flow system is like it sounds. We continuously run the reactor 24/7 and we can produce much larger volumes, at a much lower price point. Once we fire up the reactor, and optimize the system for the output, it continues producing rCF in perpetuity, or until we decide to either stop feeding it or decide to turn it off for maintenance.
This type of reactor is a much more complex system to design, but the benefits are economy of scale. We also have a really low environmental footprint because we use the energy that is generated during the processing to power the reactor.
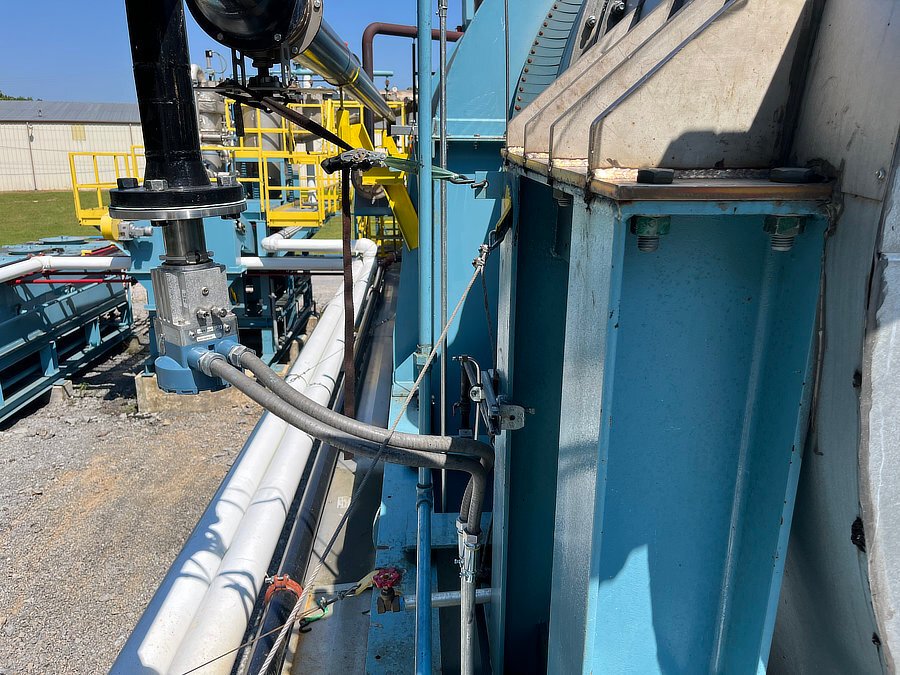
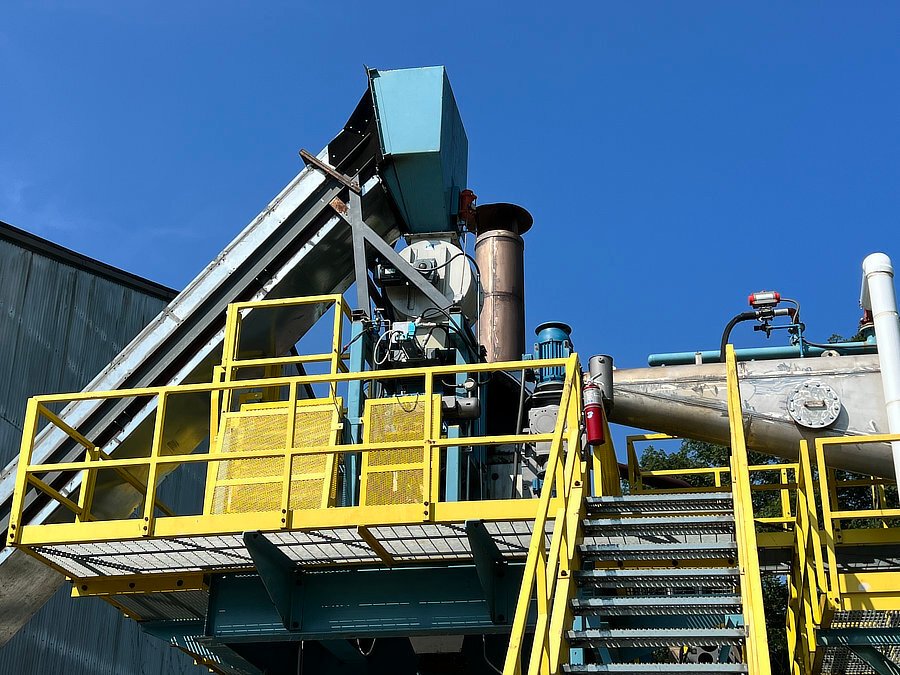

Low Price Point
We can now process an enormous amount of material in more efficient ways than a batch system could ever hope to do, and we can process any type of carbon fiber. That lowers our price, keeps the quality high, and at the same consistent rates.
The lower price point has made rCF companies viable and also created a new market for recycled carbon fiber. Carbon Fiber is lighter and stronger than steel or glass fiber, and is now much less expensive to recycle. rCF can now be used extensively in concrete to add strength, as well as to heat, as rCF is also has conductive properties. Our fiber is also used extensively in any industry that needs light and strong products such as dashboards for cars, computer cases, and airline tray tables.
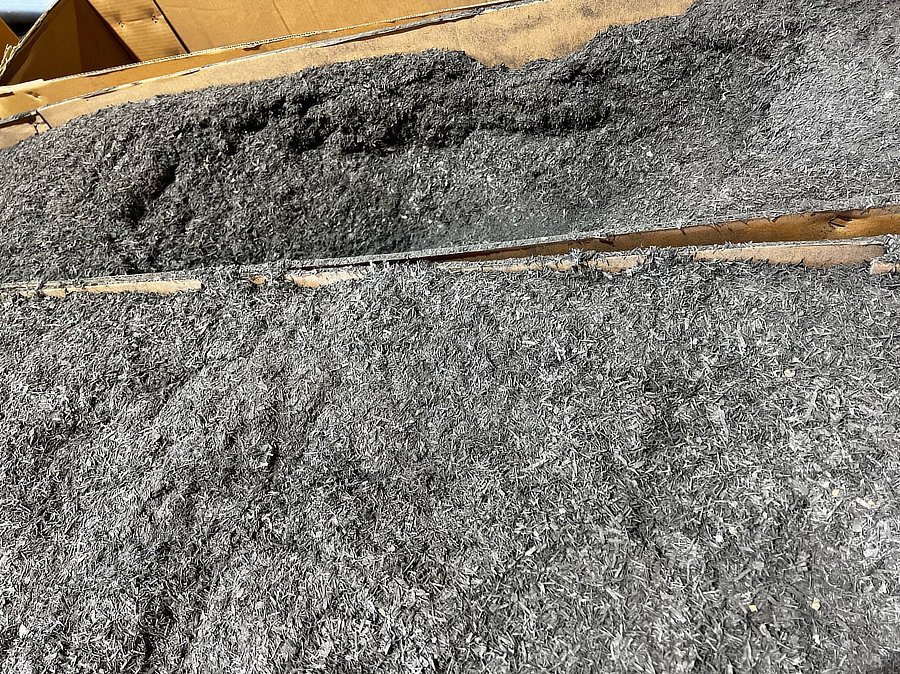
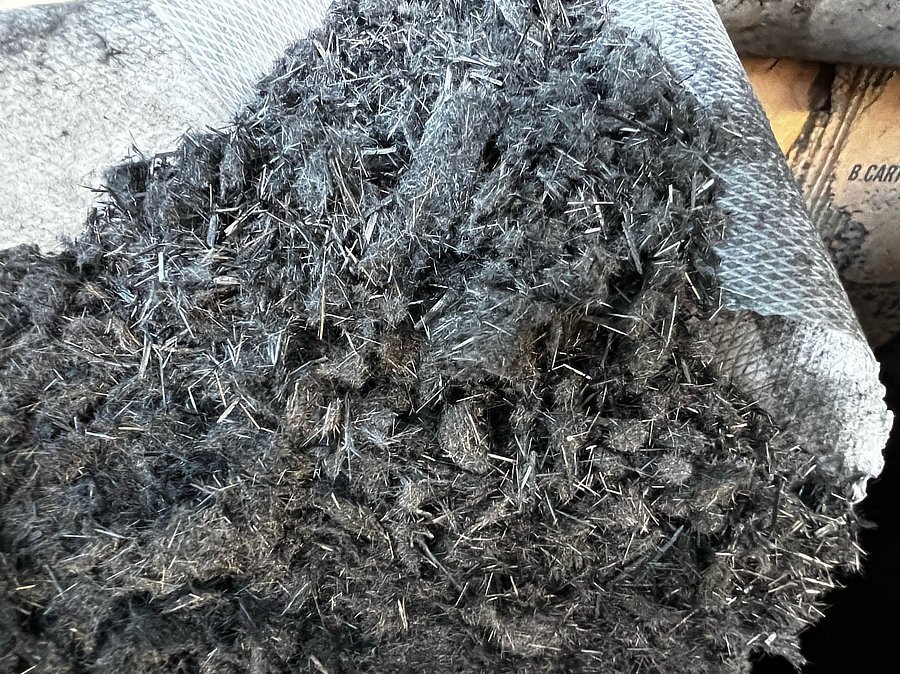
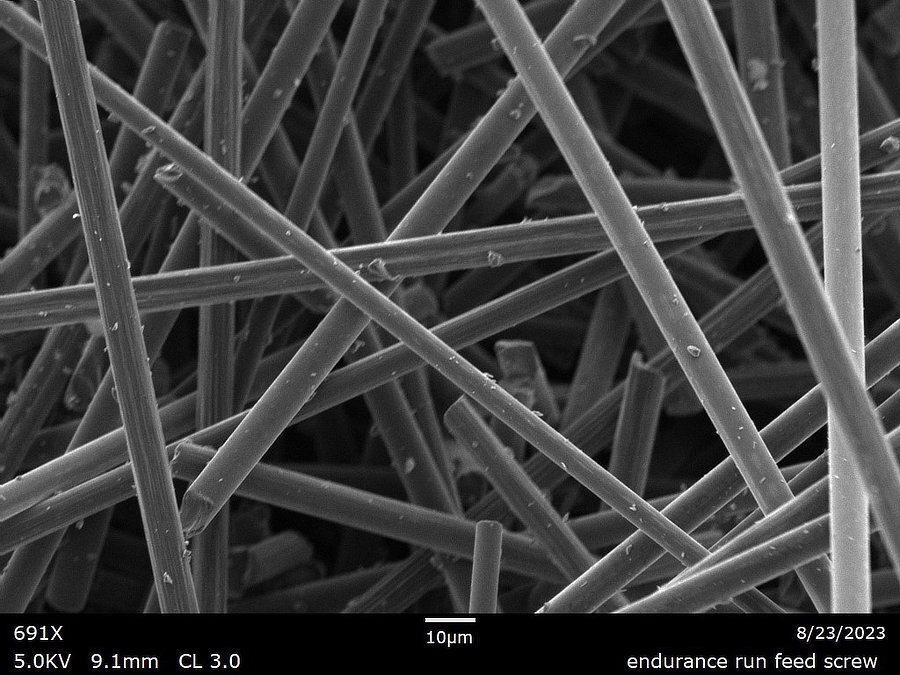
It has taken over ten years, and a lot of investment, effort, and prototyping to have these recycling capacities. We are excited to bring this revolutionary technology solution to the world, and to open new markets for rCF in unprecedented quality and quality.
See our FAQ page for more about CFR’s recycling process.